Service Plans
At Digested Organics, we provide a range of service plans designed to ensure the optimal performance and longevity of your filtration systems. Our service offerings include preventative maintenance, repairs, remote monitoring, operator training, and customized service plans to meet your specific needs.
Preventative Maintenance & Repairs
Our field service technicians are professionals with years of experience servicing pumps, valves, and other components unique to our filtration equipment. We offer:
- Preventative Maintenance: Regular check-ups and maintenance to prevent issues before they arise.
- Repairs: Prompt and efficient repairs to minimize downtime.
- Upgrades: Assistance with system upgrades to enhance performance and efficiency.
Remote Monitoring
We understand that you have a busy schedule, and managing your filtration system should be hassle-free. Our remote monitoring services include:
- Real-Time Updates: Receive real-time updates and alerts about your system’s performance.
- Scheduled Maintenance Suggestions: Timely suggestions for maintenance and cleanings.
- Operational Optimization: Continuous optimization of your system for peak performance.
Online Dashboard (DOMetrics™)
Need a quick look at how your filtration system is performing? Our DOMetrics dashboard provides:
- Summary Information: Access data such as gallons processed per day, daily operating hours, and power consumed.
- Customized Data Presentation: We work with each client to ensure all relevant data is captured and presented in a meaningful and easy-to-understand way.
Operator Training
We provide comprehensive operator training to ensure your staff can efficiently run, clean, and maintain your filtration system. Our training options include:
- In-Person Training: Hands-on training sessions at your facility.
- Online Training: Convenient remote training sessions.
- Follow-Up Training: Scheduled follow-up training as needed to reinforce knowledge and skills.
Comprehensive Service Plan (CSP)
Our Comprehensive Service Plan (CSP) is tailored to each customer’s unique circumstances and includes:
- Replacement Parts: Spiral brush filter screens, brushes, seals, and o-rings.
- Service/Repair: Maintenance of UF modules and replacement of RO membrane elements.
- Cleaning Chemicals: Provision of necessary cleaning chemicals (alkaline cleaner, acid cleaner).
- Wear Parts: Replacement of pump and sensor wear parts (e.g., pump seals, pH probe electrodes).
- Quarterly Site Visits: Regular inspections and tuning by our technicians.
- Remote Monitoring: Continuous performance monitoring by Digested Organics staff.
- 24/7 Support: Around-the-clock phone support and <24-hour technician response time.
- Online Dashboard Access: Detailed performance data and summary reports via our DOMetrics dashboard.
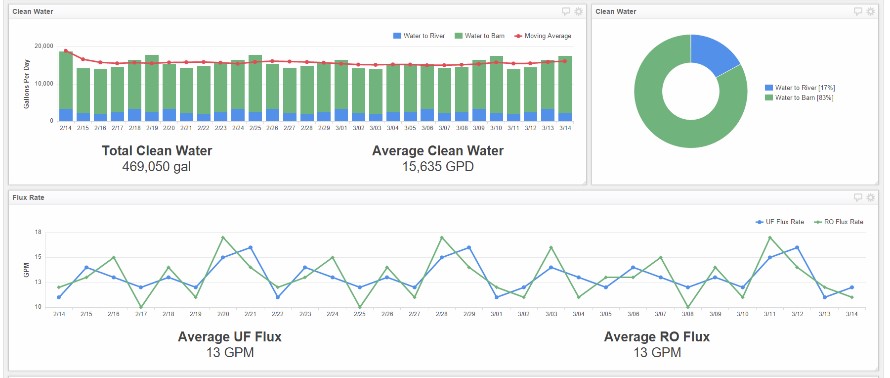
Pay-Per-Gallon Plans
For some customers, purchasing equipment may not be the best option. We offer flexible leasing and pay-per-gallon plans:
- Leasing Equipment: Ideal for short-term projects or testing equipment before scaling up.
- Pay-Per-Gallon Plans: Customers pay per gallon of liquid processed, with Digested Organics owning and operating the equipment for the duration of the contract.
Reference Articles
Fresh From The Blog
FAQs: Services & Monitoring
What services are included in the Comprehensive Service Plan (CSP)?
The CSP includes:
- Replacement parts (spiral brush filter screens, brushes, seals, and o-rings)
- Service and repair of UF modules
- Replacement of forward osmosis and reverse osmosis membrane elements
- Provision of necessary cleaning chemicals (alkaline cleaner, acid cleaner)
- Replacement of pump and sensor wear parts (e.g., pump seals, pH probe electrodes)
- Quarterly site visits for inspection and tuning
- Continuous remote monitoring of system performance
- 24/7 phone support and <24-hour technician response time
- Access to our online dashboard (DOMetrics) for detailed performance data and summary reports
What is remote monitoring and how does it benefit me?
Remote monitoring involves Digested Organics staff continuously observing your system’s performance in real-time. Benefits include:
- Immediate updates and alerts about system performance
- Suggestions for scheduled maintenance and cleanings
- Operational optimization to ensure your system runs at peak performance
- Reduced need for on-site management and troubleshooting
How does the Online Dashboard (DOMetrics) help me manage my system?
The DOMetrics dashboard provides:
- Summary information on gallons processed per day, daily operating hours, and power consumed
- Customized data presentation to ensure all relevant information is captured and easily understood
- Access to detailed performance data and summary reports, allowing you to monitor your system’s performance effectively
What training options are available for operators?
We offer comprehensive operator training, including:
- In-person training sessions at your facility
- Online training sessions for remote learning
- Scheduled follow-up training as needed to reinforce knowledge and skills
Our training ensures your staff can efficiently run, clean, and maintain your filtration system.
What is the difference between leasing equipment and pay-per-gallon plans?
- Leasing Equipment: Ideal for short-term projects or testing equipment before scaling up. Leasing includes operating assistance from Digested Organics personnel.
- Pay-Per-Gallon Plans: Customers pay per gallon of liquid processed. Digested Organics owns and operates the equipment for the duration of the contract, providing a hassle-free solution for your wastewater management needs.
How often are site visits conducted under the CSP?
Under the Comprehensive Service Plan, our technicians conduct quarterly site visits for inspection and tuning of your system. These regular visits ensure that your system remains in optimal working condition.
What kind of support is available if my system goes down?
We offer 24/7 phone support and guarantee a technician response time of less than 24 hours if the system goes down and cannot be fixed remotely. This ensures minimal downtime and quick resolution of any issues.
How can I determine which service plan is right for my facility?
To determine the best service plan for your facility, consider factors such as the volume and type of wastewater you need to treat, your operational budget, and your specific needs for maintenance and monitoring. Consulting with our experts at Digested Organics can help you assess your requirements and select the appropriate plan.