High-Throughput Continuous Screen Technology
Discover the efficiency and reliability of the Spiral Brush Screen Filter, a cutting-edge solution designed to enhance your wastewater treatment process. Our high-throughput continuous screening technology ensures optimal performance and durability, setting a new standard for solids separation and filtration efficiency. Ideal for various applications, this filter system is engineered to meet the demands of modern wastewater management.
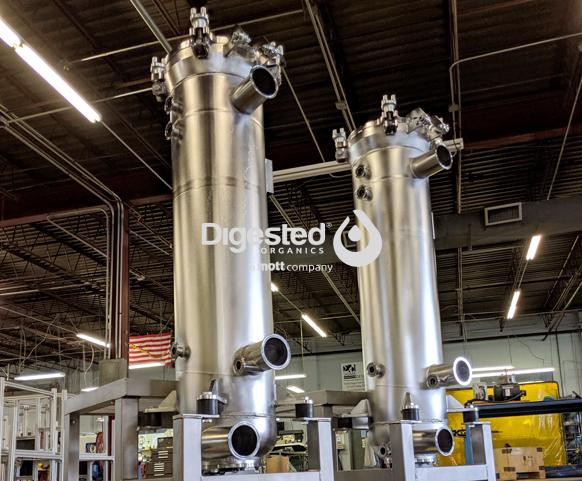
KEY FEATURES
Automatically Self-Cleaning
Handles High and Variable TSS (25,000+ mg/L)
Low Cost / Low Maintenance
Continuous Filtrate with up to 99%+ Recovery
Patented Technology
Single units or Multiplex
Versatile Applications for Wastewater Management
The Spiral Brush Screen Filter is exceptionally suited for a wide range of wastewater management needs, from the food and beverage industry to agricultural effluents in manures and lagoons, and even for irrigation systems. Its design efficiently handles high-load wastewater, offering a sustainable and effective solution for solids separation and improved water quality across diverse sectors.
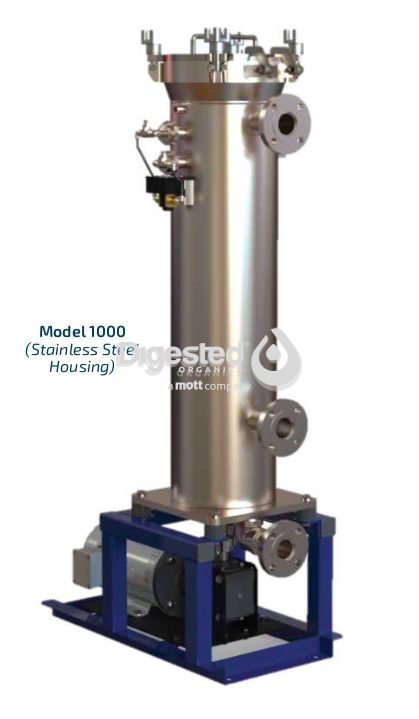
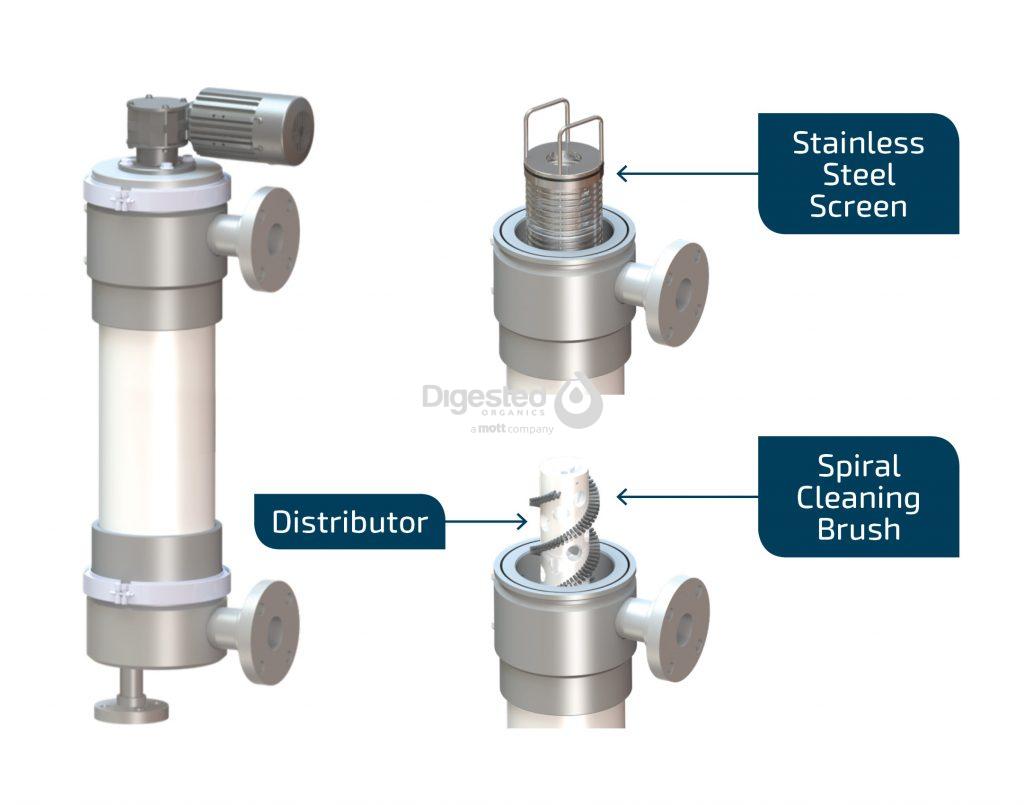
How The Spiral Brush Screen Filter Works
In the Spiral Brush Screen Filter system, wastewater enters the screen from the top, separating solids inside the cylindrical screen as clean water passes through. A motor-driven spiral brush continuously cleans the screen, transporting solids to a purge outlet. This process allows for uninterrupted operation without the need for backwashing, ensuring efficient filtration and disposal of solids.
Multiplex Skids
The Spiral Brush Screen Filter’s versatility and efficiency are further enhanced by our customizable multiplex skids, designed to meet a range of operational needs and settings:
- Availability of 1 to 4 units per skid, with material options of powder-coated steel or stainless steel.
- Stainless steel screens ranging from 10 to 100 microns for tailored particle size removal and throughput.
- Features custom-engineered plastic brushes within the screens, supported by high-efficiency motors.
- Incorporates isolation valves for selective maintenance without disrupting service.
- Equipped with a water inlet valve for system flushing, a maintenance-friendly platform with non-slip grating, and NEMA 4X enclosures with HMI for simplified operations.
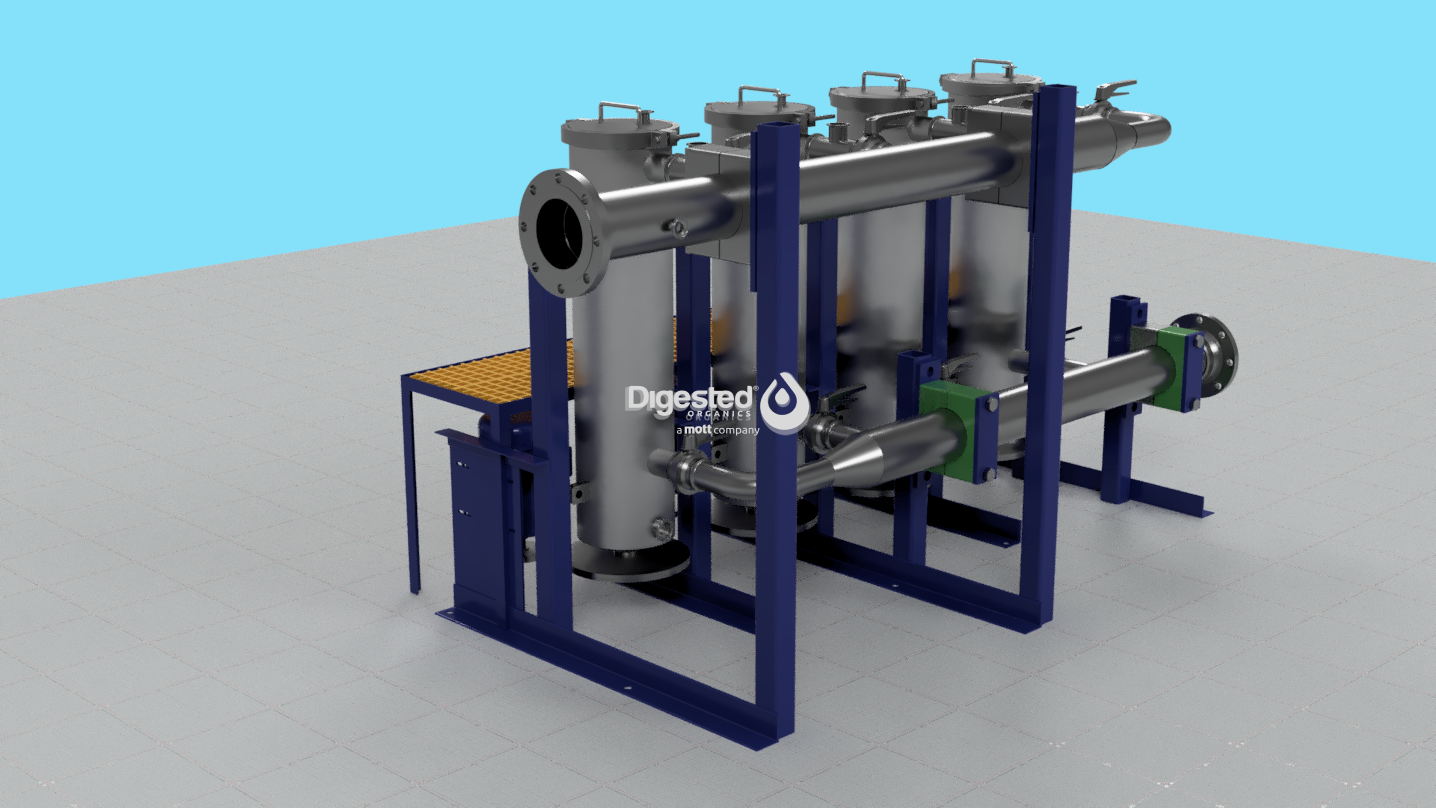
Equipment Options
Model 850
- Inlet: 2” FNPT or #150 Flange
- Filtrate Outlet: 2” FNPT or #150 Flange
- Purge Outlet: 2” FNPT or #150 Flange
- Max Flow: 100 gpm
- Screen Micron Rating: 15 – 100 micron (wedgewire type)
- Max Operating Pressure: 120 psi @70°F
- Max Temp: 190°F
- Head Loss: 1-3 psi)
- Brush Motor: 1 HP (460V, 3-Ph)
- Wetted Housing: CPVC, 2205SS, Acetal
- Seals: EPDM or Viton
- Cleaning Brush: Acetal, Nylon 6.12 & 316 SS
- Filter Element: 316L SS
Model 1000
- Inlet: 3” FNPT, Flange, or Tri-Clamp
- Filtrate Outlet: 3” FNPT, Flange, or Tri-Clamp
- Purge Outlet: 3” FNPT, Flange, or Tri-Clamp
- Max Flow: 250 gpm
- Screen Micron Rating: 15 – 100 micron (wedgewire type)
- Max Operating Pressure: 150 psi @70°F
- Max Temp: 190°
- Head Loss: 1-3 psi
- Brush Motor: 7.5 HP (460V, 3-Ph)
- Wetted Housing: 316 SS
- Seals: EPDM or Viton
- Cleaning Brush: Nylon 6.12, 316 SS, UHWM-PE
- Filter Element: 316L SS
APPLICATIONS
Wastewater clarification
Suspended solids removal
Food and beverage manufacturing wastewater
Flush manure clarification
Brewery wastewater clarification
Pre-filtration for existing UF or RO system or our own Forward Osmosis™
Enhancing Wastewater Management with the Spiral Brush Screen Filter
The Spiral Brush Screen Filter is a pivotal solution designed for effective wastewater treatment. This innovative system is engineered to remove solids from liquids, making it ideal for various industries, including food and beverage production and agricultural applications. Its unique spiral brush mechanism ensures continuous, efficient operation, reducing maintenance needs and enhancing overall filtration efficiency. This filter represents a step forward in sustainable wastewater management practices.
PLEASE CONTACT US TODAY TO LEARN ABOUT AVAILABLE PILOT TESTING IN-HOUSE AND RENTAL UNITS.
Reference Articles
Fresh From The Blog
FAQs: Spiral Brush Screen Filters
What is a Spiral Brush Screen Filter?
A Spiral Brush Screen Filter is an advanced filtration system designed to remove solids from wastewater efficiently, utilizing a spiral brush mechanism to maintain cleanliness and flow.
How does the Spiral Brush Screen Filter work?
It operates by directing wastewater through a cylindrical screen, where a motor-driven spiral brush continuously removes debris, allowing for uninterrupted filtration and disposal of solids.
What are the key benefits of using a Spiral Brush Screen Filter?
The key benefits include improved water quality, reduced maintenance due to its self-cleaning mechanism, and high efficiency in solids removal, making it ideal for various industrial applications.
Can the Spiral Brush Screen Filter be used in agricultural applications?
Yes, it is particularly effective in agricultural settings, including manure management and irrigation systems, due to its ability to handle high-load wastewater and enhance water recycling processes.